MoSx-Dünnschichten für fluidfreie Schmierstoffsysteme
Molybdändisulfid (MoS2) stellt einen etablierten Festschmierstoff dar, welcher aufgrund seiner hexagonalen Gitterstruktur das leichte aufeinander Abgleiten der Basalebenen ermöglicht. Diese Stapelung von „Sandwich“-Lamellen beinhaltet jeweils eine Lage aus Molybdän(Mo)-Atomen, welche sich zwischen zwei Lagen aus Schwefel(S)-Atomen befindet, sodass jedes Mo-Atom von sechs S-Atomen umgeben wird, die an den Ecken eines regelmäßigen Oktaeders lokalisiert sind. Hier liegt zwischen Mo und S eine starke kovalente Bindung vor, wobei die zwischen den S-Mo-S-Lamellen schwache van-der-Waals-Bindung die geringe Scherkraft und somit minimale Reibungskoeffizienten ermöglicht.
Mittels PVD-Beschichtungsverfahren lassen sich MoS2-basierte Dünnschichten auf Bauteilen und Komponenten synthetisieren, um das Potential der geringen Reibung für fluidfreie Schmiersysteme zu nutzen. Aufgrund der Synthesebedingungen variiert das S/Mo-Verhältnis, weshalb bei nicht-stöchiometrischen Zusammensetzungen üblicherweise die Schreibweise MoSx verwendet wird. Mit der Kathodenzerstäubung abgeschiedene MoSx-Dünnschichten zeichnen sich durch eine nadelförmige Topographie und eine poröse kolumnare Morphologie aus (siehe Abb. Unten).
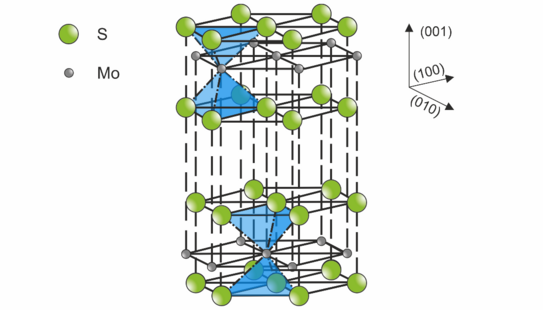
Eine polykristalline Struktur ist dabei charakteristisch mit den hauptsächlichen Orientierungen entlang der (110)- und (100)-Randebenen sowie der (002)-Basalebene, welche neben dem S/Mo-Verhältnis maßgeblich das Reibungs- und Verschleißverhalten der Dünnschicht bestimmt. Die Basalebene ruft eine Orientierung senkrecht zur Belastungsrichtung hervor, sodass die stärkste Zugspannungsfeldkomponente parallel zur Oberfläche verläuft, auf der sich äußerst stabile chemische Bindungen befinden. Damit stellt sie auch den Hauptgrund für Steigerungen der mechanischen Kennwerte wie Härte und E-Modul dar.
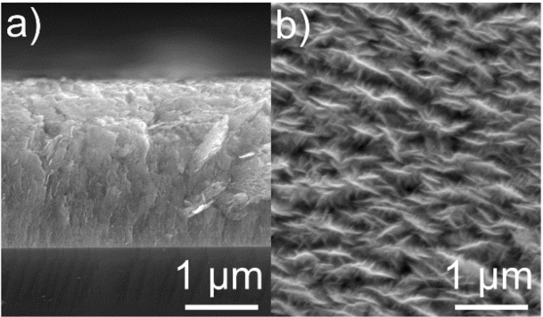
MoSx-Dünnschichten besitzen ausgezeichnete tribologische Eigenschaften im Vakuum. Dank seiner chemischen Adhäsion auf Metallen bildet MoSx neben dem Tribofilm auf der Schichtoberfläche auch einen Transferfilm auf dem Gegenkörper. Die selbstordnende, lamellare Struktur ermöglicht eine effektive Schmierung, da MoSx durch chemische Adhäsion in der (002)-Basalebene am Metallgegenkörper haftet und durch die parallele Ausrichtung der Schichten entlang der Gleitrichtung einen geringen Scherwiderstand bietet. Im Ultrahochvakuum und in trockener Stickstoffatmosphäre erreichen MoSx-Dünnschichten extrem niedrige Reibungskoeffizienten von etwa μ = 0,003, da die Kristallite in der (002)-Basalebene ausgerichtet sind.
Dadurch entstehen sehr gleitfähige Bedingungen ohne tribochemische Reaktionen, dessen Produkte wie bspw. Oxide die Reibung erhöhen könnten. Feuchte Umgebungen hingegen verschlechtern die Schmierwirkung erheblich.
Bereits bei 40 % Luftfeuchtigkeit erhöht sich der Reibungskoeffizient auf μ = 0,15 bis 0,20, da H2O-Moleküle zwischen die MoSx-Scherebenen eindringen, was die Adhäsion und somit die Scherfestigkeit steigert. Zudem fördert Feuchtigkeit die Oxidation zur Bildung von MoO₃, sodass die schmierende Wirkung weiter reduziert wird. Auch die Auflagekraft beeinflusst die Reibung. Höhere Kräfte reduzieren den Wassereinfluss, senken den Reibungskoeffizienten, verkürzen aber die Lebensdauer der Schicht. In trockenen Bedingungen bleibt der Reibungskoeffizient konstant niedrig, unabhängig von der Auflagekraft.
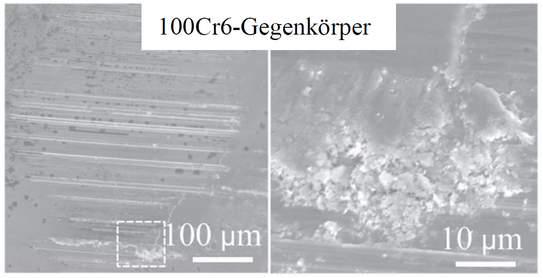
Elementmodifikationen von MoSX-Dünnschichten
Aufgrund der verringerten tribologischen Leistungsfähigkeit in feuchter Umgebungsatmosphäre ergeben sich für trockenlaufende und unsynchronisierte Schraubenrotoren mit einer reinen MoSX-Beschichtung höhere Reibungskoeffizienten, welche wiederum erhöhte Verschleißschäden hervorrufen. Durch die gezielte Modifikation dieser Dünnschichten mit ausgewählten Elementen wie Wolfram (W), Silber (Ag), Kupfer (Cu), Stickstoff (N) oder Kohlenstoff (C) können die tribo-mechanischen Eigenschaften der MoSX-Dünnschichten nachweislich beeinflusst werden. Im Zuge dessen ordnen sich bspw. die Kristallite in der bevorzugten (002)-Basalebene an oder die Bildung des Transferfilms wird verstärkt, sodass sich ein verbessertes Reibverhalten und eine höhere Verschleißbeständigkeit ausbildet.
In der nachfolgenden Abbildung sind REM-Aufnahmen von verschiedenen Modifikationen mit W, Ag und C der MoSX-Dünnschichten nach Tribometerversuchen mit einem 100Cr6-Gegenkörper dargestellt. Das darunterliegende EDX-Mapping der Schichtelemente soll verdeutlichen, ob und inwiefern sich noch Schichtmaterial in der Verschleißspur befindet und welche Elemente in dem Tribofilm hauptsächlich vorliegen. Während die W-Modifikation mit 11,1 At.-% sowie die Ag- und C-Modifikationen eine schmalere Verschleißspur und geringere Reibung erzielen, steigt der Reibungskoeffizient bei einem erhöhten W-Anteil enorm an und bewirkt eine breitere Verschleißspur als die des reinen MoSX. Infolge der präzisen Anpassung der Anteile der Modifikationselemente zeigen sich demnach verminderte Reib- und Verschleißmechanismen, was eine effizientere Ressourcennutzung im Hinblick auf trockenlaufende und unsynchronisierte Schraubenrotoren begünstigt.

Anwendungsbeispiele für MoSx-basierte Dünnschichten:
-
Raumfahrttechnik (Schmierstoffe für Satelliten und Weltraumteleskope)
-
Präzisionslager und Vakuumtechnik (z. B. in Halbleiterfertigung)
-
Hochleistungsgetriebe und Maschinenkomponenten unter extremen Bedingungen
-
Mikroelektromechanische Systeme (MEMS) zur Reibungs- und Verschleißreduktion
Verfasst von Dominic Graf, 07.02.2025